Laser battle that gave Europe our Aeolus wind-mapper
It passes over at us at local dawn or dusk: among the most ambitious lasers ever flown in space, shining down to map Earth’s otherwise unknown global wind field. ESA’s Aeolus mission took more than two decades to reach this point. The laser was a key technology: in testing, the intensity of its beam was actually destroying the laser’s optical elements – the mission could not fly until this problem was fixed.
“Today Aeolus is returning more wind data than all ground-based measuring systems put together,” says Errico Armandillo, retired head of ESA’s Opto-electronics section. “But it took the sustained efforts of ESA labs and technical experts – in close cooperation with the Aeolus team – to make it fly.
“In the end we had to set up two new labs, call in additional DLR German Aerospace Center support and produce entire new technical standards, which are now being applied to all follow-on laser missions. The commercial space industry by itself could not have gone to the lengths we took.”
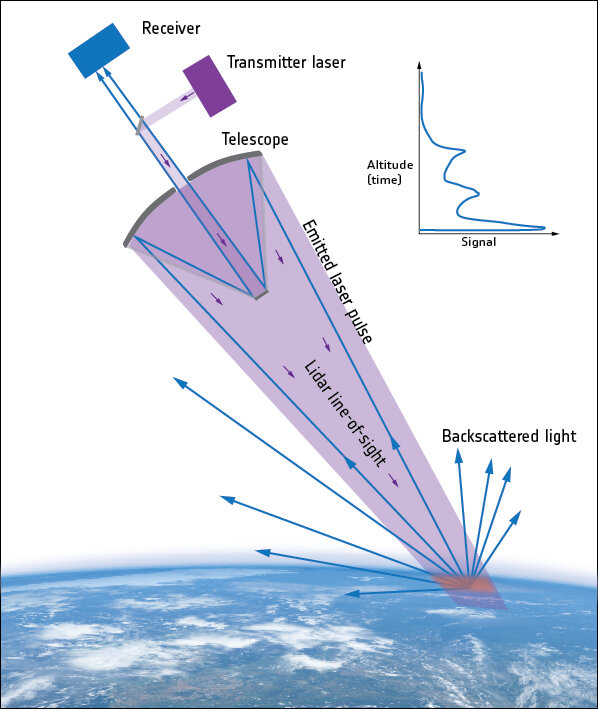
At the heart of Aeolus – an ESA Earth Explorer mission that launched on 22 August – is the Atmospheric Laser Doppler Instrument, or Aladin. This is an ultraviolet lidar – ‘laser radar’ – whose 50 pulses per second are magnified by a 1.5-m-diameter telescope to shine through the entirety of the atmosphere from 320 km away in space.
Within three one-thousandths of a second, this same telescope then gathers up the resulting laser backscatter from aerosol droplets, water vapour and actual air molecules across different atmospheric layers. On the same basis as a police radar gun, this backscatter’s ‘Doppler shift’ is measured to derive wind velocities down to a few metres per second, taking a fresh sample every 200 km.

Making a laser this intense was not straightforward. When a prototype version of Aladin was run, its laser optics degraded by 50% in less than six hours of operations. This was bad news for a proposed three-year mission, but solving the problems created new technology to benefit a range of future missions.

Lining up laser technology
Attempts to understand and forecast the wind date back to Aristotle in the 4th century BC. Today, wind profiles sampled down through the atmosphere are an essential element of accurate medium- to long-term weather forecasting, as well a key input for modelling climate change.
Previously, this information was simply not available: the best equivalent came from ground-based sensors, aircraft and balloon-based radiosondes giving localised point measurements, which were then extrapolated through cloud tracking or computer simulations. Aeolus in orbit changes that: for the first time in history, wind fields can be mapped globally, on a three-dimensional basis.

The idea of flying a wind-surveying lidar in orbit dated back to the early 1980s, considered at one time for the International Space Station. This lidar technology was later applied to spacecraft rendezvous and docking for ESA’s ISS-supplying ATV cargo spacecraft.
Following the 1989 recommendation of ESA’s space laser working group a high-energy carbon dioxide gas laser was developed, then demonstrated for aerial lidar. Later, in the mid 1990s, the development of spaceworthy laser-pumping diodes opened the way to a more compact solid-state version. The then ‘Aeolus Atmospheric Dynamics Mission’ was accordingly planned for a post-2000 flight.

“Aeolus’s Aladin runs on a synthetic crystal ‘ND: YAG’ laser, a common pulsed-laser ‘workhorse’,” explains ESA laser engineer Linda Mondin. “This crystal emits infrared laser light. A pair of what we call ‘non-linear crystals’ subsequently convert this first into the green region of the visible spectrum then to the shorter ultraviolet wavelength we require.”
Selecting high-energy ultraviolet was extremely ambitious, but essential to achieve a detectable level of backscatter from air molecules, along with lower-altitude aerosols and dust (it also prevented any eye damage risk from visible wavelengths). Ultraviolet is also the wavelength of greatest ‘Rayleigh scattering’ – the shifting of light by air that makes the sky blue.
So far, so good, recalls Errico: “We designed the UV laser to operate in vacuum, which simplified its thermomechanical design – considering we needed to maintain our lens alignment precisely. Except it was then our tears began.”

Laser lights going out
The first inkling of trouble began with the early failure in orbit of NASA’s 2003-launched IceSAT, built around an ice-mapping lidar instrument. At the same time, Aladin ground testing hit parallel problems, dominated by laser-induced contamination.
Organic contaminants from the Aladin laser equipment – akin to the fumes giving a new car its smell – were being carbonised by the UV laser, accumulating on its lenses. These growing deposits then absorbed the laser heat, distorting and eventually darkening the carefully crafted optics. ESA and wider European laser experts began to probe the phenomenon.
“The first solution was to take extreme precautions to remove all organics,” adds Errico. “But this did not prove entirely possible – even metal surfaces can act as a source. Even at just a few parts per billion of organics, contamination was still introduced.”

For clues the team reached out to terrestrial UV laser users, such as France’s Laser Mégajoule facility – employed to ignite nuclear fusion reactions – as well as the semiconductor industry.
“The answer?” says Linda. “Simply a pinch of air. Injecting a small amount of oxygen allows the contamination to burn up in the laser heat, cleaning the lens. In testing we saw this work in a matter of minutes.”
A breath of fresh air
Rather than redesigning Aladin to work on a fully pressurised basis, small wisps of oxygen are released from a pair of 30 litre tanks. This oxygen flows close to the optical surfaces that see the UV light, then gradually leaks out of the instrument enclosure.

Access the video
“Just like us, the laser has to breathe,” adds Linda. “It’s very elegant because the burnt up contaminants flow out of the instrument along with this oxygen, in the form of carbon dioxide and water. We need roughly 25 Pascals of residual oxygen pressure – just one four-thousandth of standard atmospheric pressure.”
Contamination was only one of numerous challenges the instrument faced. The copious amounts of heat produced within the 30 litre volume of the laser transmitter demanded removal: this was done using ‘heat pipes’, which cool the laser by evaporating liquid and moving it to a space-facing radiator – analogous to human sweat glands. And Aladin’s electronics needed to operate on a steady, constant basis throughout their planned four billion laser shots.
“There were so many ways it could go wrong, we were worried,” adds Errico. “And then it worked! Those first wind profiles felt like Christmas coming early, a really amazing gift.”

Aladin’s development has given ESA its world-leading Optics and Opto-Electronics Labs, along with a set of ISO-certified laser development standards for other laser-based missions, starting with the EarthCARE mission for clouds and aerosol monitoring. These might also include further Aeolus satellites, favoured by the European Centre for Medium-Range Weather Forecasts, the mission’s main customer.
“It’s proved an extremely complex mission, and we’ve learnt an awful lot about lasers,” concludes Linda. “Achieving success has really been a team effort, with the different ESA Directorates and industry rowing in the same direction against a really strong wind.”
“The fact we have a high-power UV laser instrument now working in space is testament to all of the hard work, ingenuity and inventiveness of many dedicated engineers both in industry, ESA and elsewhere,” comments Denny Wernham, Aeolus’s instrument manager.
“Within all this, the contribution of ESA’s Directorate of Technology, Engineering and Quality has been invaluable, setting up a dedicated laboratory to demonstrate the self-cleaning method we eventually utilised on the mission, and also proving the ability of Aladin’s optics to withstand its high-laser intensities for the mission lifetime.
“Aeolus is a world first mission that will hopefully lead to many active laser missions in the future and shows the true value of close collaboration between industry and ESA to find innovative solutions to very tough technical challenges.”