Ariane 6 on the way to flight
This has been an intense year for Ariane 6 development, with progress boosted across Europe: plants are manufacturing new parts using novel methods, all engines have been tested, and the construction of launch facilities is well underway.
ESA has worked with an industrial network led by prime contractor ArianeGroup, of more than 600 companies in 13 European countries, including 350 small- and medium-sized enterprises, to fine-tune the design and start production. Meanwhile, France’s CNES space agency has been preparing its launch facilities at Europe’s Spaceport in French Guiana.
Details on all these activities were recently shared at the 69th International Astronautical Congress in Bremen, Germany – downloadable here (.pdf) – along with two papers submitted to the congress: launch system (.pdf) and launcher system (.pdf), here are the highlights.
Europe’s launcher for a new decade
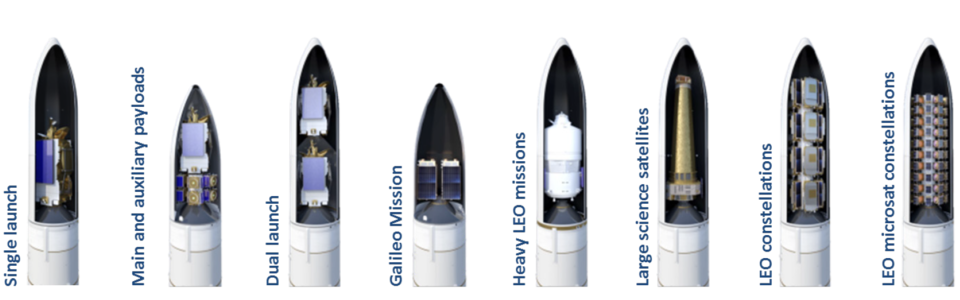
Europe’s new Ariane 6 launcher covers a broad range of commercial and institutional applications while dramatically decreasing the cost of launches compared to Ariane 5.
Enabled by ESA’s Light satellite Low-cost Launch opportunity Initiative, a multiple launch service for small satellites starting mid-2021 will offer cost-effective launch opportunities for satellites of under 400 kg, via a rideshare approach on launchers such as Ariane 6, and its smaller cousin Vega-C.
The Ariane 6’s core stage is powered by Vulcain 2.1, an upgraded engine derived from Ariane 5’s Vulcain 2; its upper stage is powered by the reignitable Vinci engine. Two or four P120C solid-fuel boosters for Ariane 6, common with Vega-C, will be strapped on to provide thrust at liftoff.
The P120C and Vulcain 2.1 development models have started their ground testing, the Vinci is now qualified. This leads to the next significant milestone: the delivery of the Ariane 6 qualification model, to start combined tests in French Guiana at the end of 2019.
The second P120C model will be tested in French Guiana early next year, to verify its design and performance.
The Ariane 6 upper stage will be tested at the DLR German Aerospace Center newly developed P5.2 test facility in Lampoldshausen at the end of 2019.
Specialist factories have started production
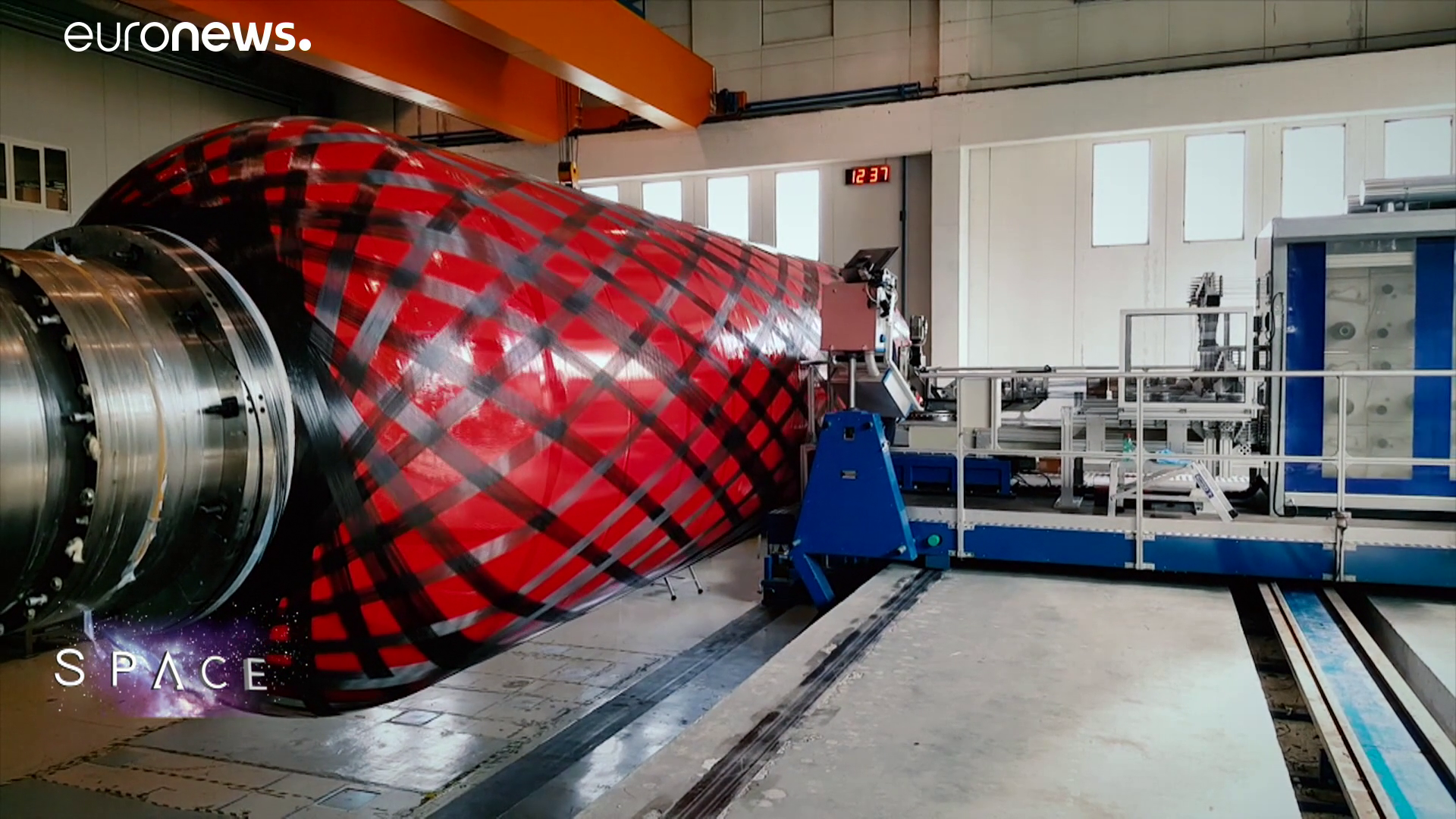
Access the video
Casings for the P120C boosters are formed from specially developed carbon composite fibre, which is wound at Avio’s Colleferro factory in Italy.
The nozzles for the boosters will be produced at a rate of 35 per year from a highly automated facility opened in July in Le-Haillan, France.
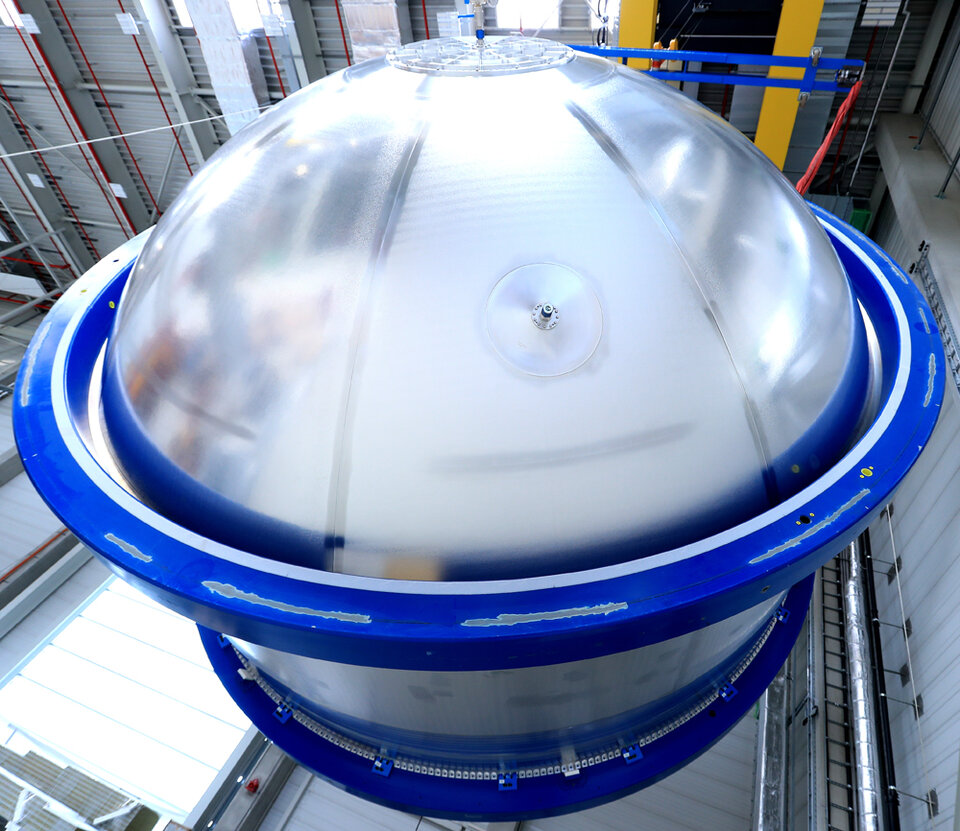
This April, MT-Aerospace – one of the main industrial partners of ArianeGroup on the Ariane 6 project – integrated the first hydrogen tanks of Ariane 6’s upper stage liquid propulsion module at their Bremen, Germany, facility.
Airbus Defence and Space opened a facility this month in Oegstgeest, the Netherlands, to develop, build, test and qualify the engine frames for the Vulcain and Vinci engines. The Vinci frame will be transported to Bremen. The Vulcain frame will be sent to Les Mureaux, France, for final assembly with the Ariane 6 core stage.
By the end of this year the ArianeGroup facility in Les Mureaux – hosting the largest friction stir welding machines in Europe – will be poised to begin producing the Ariane 6 cryogenic tanks at a rate of seven to eight stages at a time for Ariane 6’s lower liquid propulsion module.
Testing the limits of Ariane 6 propulsion
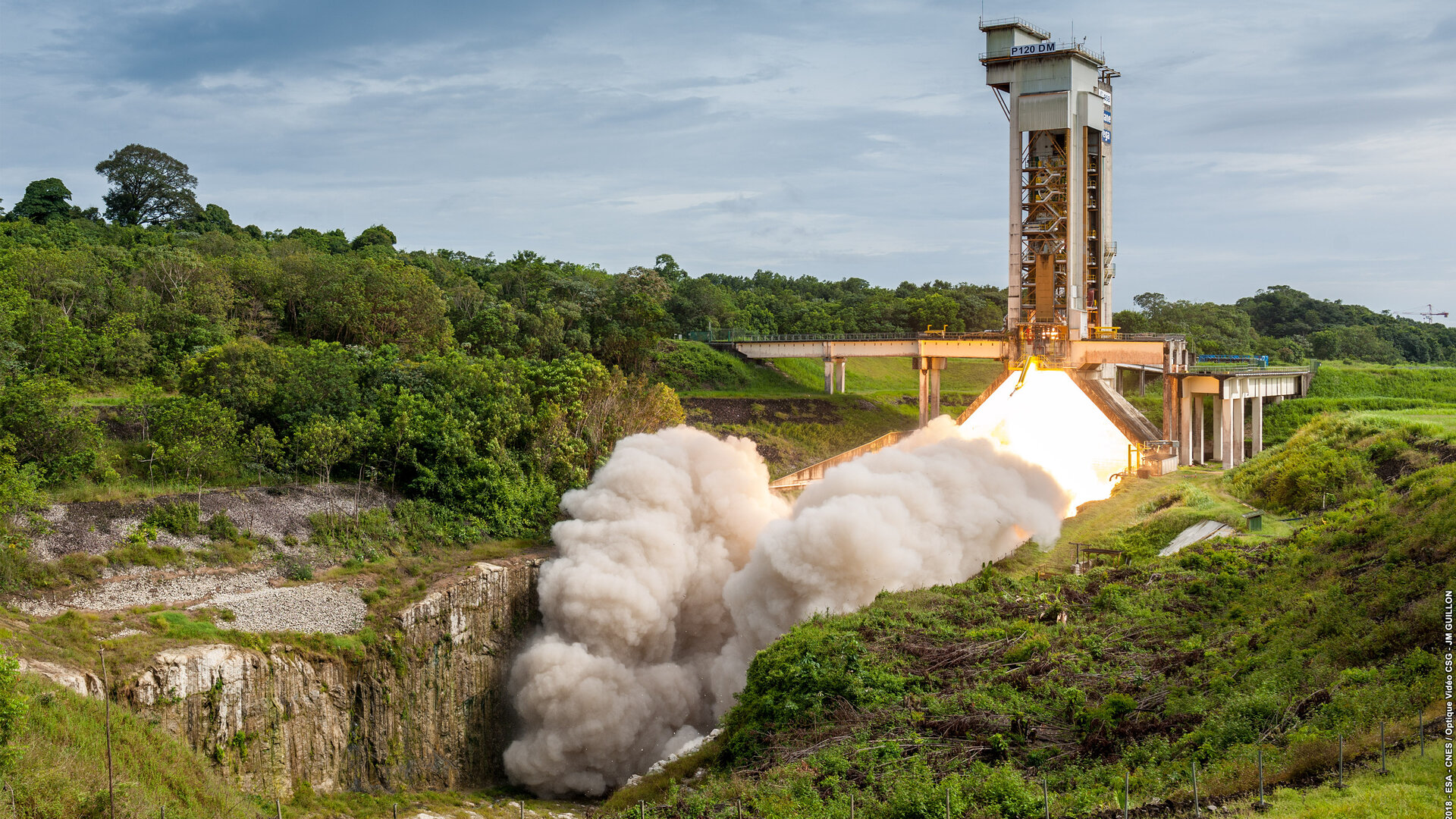
Access the video
Testing is about stretching the limits of performance to gain a detailed understanding of how components work, not just under normal operating conditions but also at higher temperatures, pressures, and with different fuel mixtures.
The P120C booster underwent hot firing at Europe’s spaceport in French Guiana in July 2018. In 135 seconds it burned 142 tonnes of propellant.
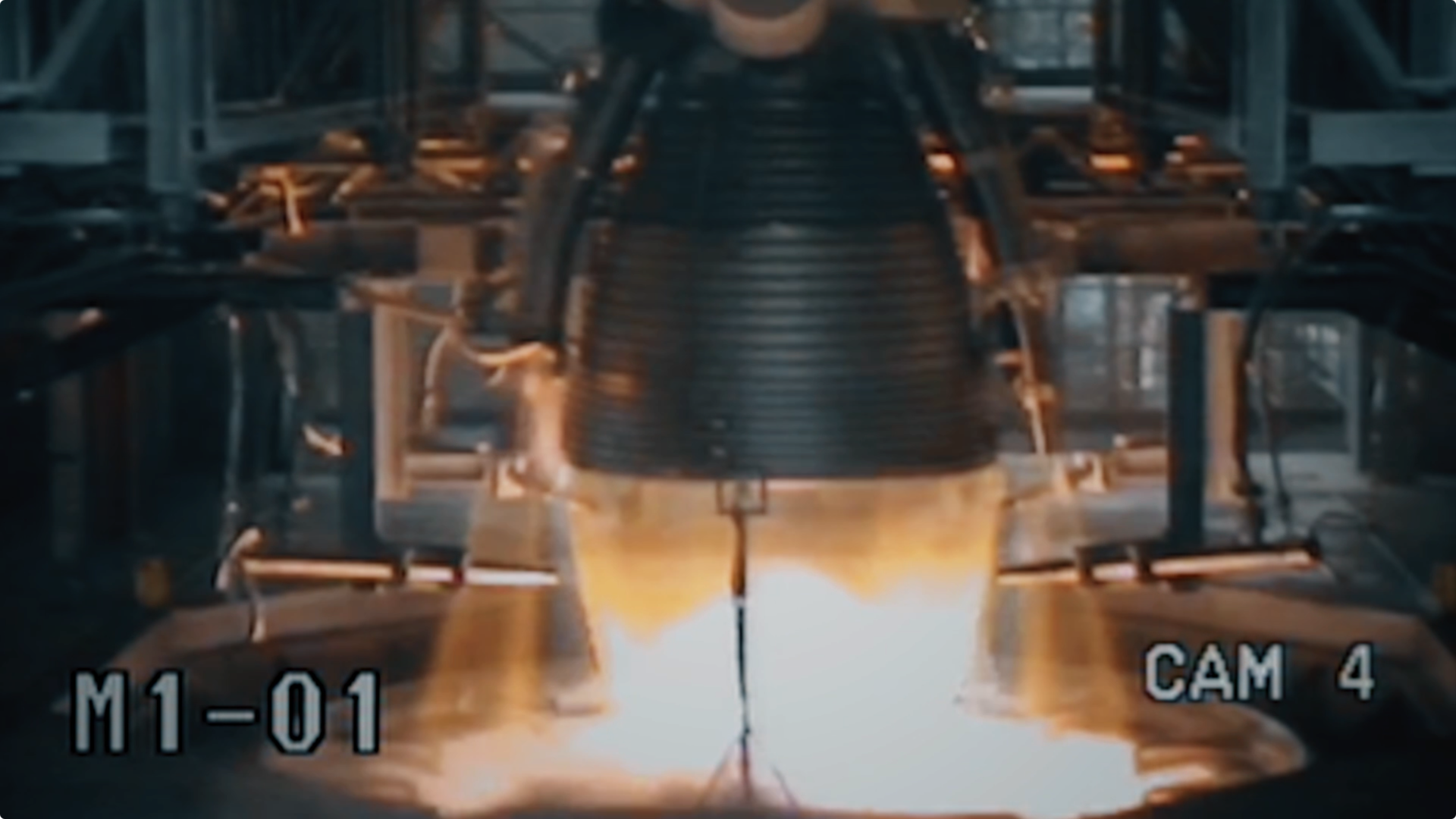
Access the video
The Vulcain 2.1 engine will help to propel Ariane 6 in the first 10 minutes of flight, up to an altitude of 200 km, delivering 135 tonnes of thrust in vacuum. It has a simplified and more robust nozzle, a 3D-printed gas generator, and a heater for oxygen tank pressurisation.
The test campaign started in January with the first test firing at the DLR German Aerospace Center test facilities in Lampoldshausen. A total of 11 successful subsequent tests of the engine brought its total accumulated burn time to over 105 minutes. The second test campaign began in October.
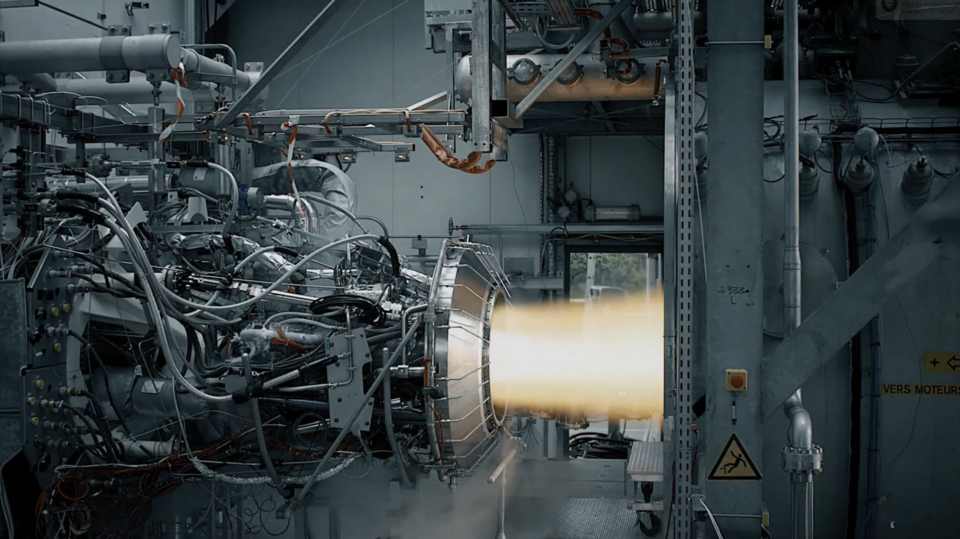
Vinci is the re-ignitable engine of the upper stage that increases the operational flexibility of Ariane 6 and ensures that the engine safely deorbits at the end of the mission.
This engine was successfully tested more than 140 times and reignited multiple times in succession in near vacuum to complete its qualification. Final testing in October brought a total of more than 14 hours of operation.
Launch facilities taking shape at Europe’s Spaceport
About 600 people are currently employed in the construction of the Ariane 6 launch pad, which is 28.5 metres deep and 200 metres wide, formed with enough concrete to fill 67 Olympic sized swimming pools – approximately 167,500 cubic m.
In September, the 700 tonne launch table that will support Ariane 6 at launch was positioned on the launch pad (read more).
The 8200 tonne mobile gantry that will store and protect Ariane 6 until it is retracted five hours before each launch, is currently being erected.
The steel deflectors that will funnel the fiery plumes of Ariane 6 into the exhaust tunnels at liftoff will soon be installed at the base of the launch pad (read more).