ATV Integrated Cargo Carrier
Powered by the ATV Service Module, the Integrated Cargo Carrier (ICC) made up 60 percent of ATV's total volume.
It was the store room of an ATV with a maximum capacity of 6.6 tonnes of cargo.
The Integrated Cargo Carrier carried two kinds of cargo:
- dry cargo, such as critical hardware equipment, was stored in the spacious pressurised part of the Cargo Carrier, which was accessed by the astronauts.
- fluid cargo such as refuelling propellant for the Station was stored in the non-pressurised part of the Cargo Carrier, to the rear. Their contents were transferred through pipes to the Station's own plumbing or through manually operated hoses.
The Integrated Cargo Carrier was designed in two parts:
- the pressurised module docked to the Space Station and held the hatch connecting the two spacecraft
- A non-pressurised part, making up 10 percent of the total volume was located at the rear
The 48 m³-pressurised section of the Cargo Carrier had room for up to eight standard racks which were designed with modular aluminium elements to store equipment and transfer bags.
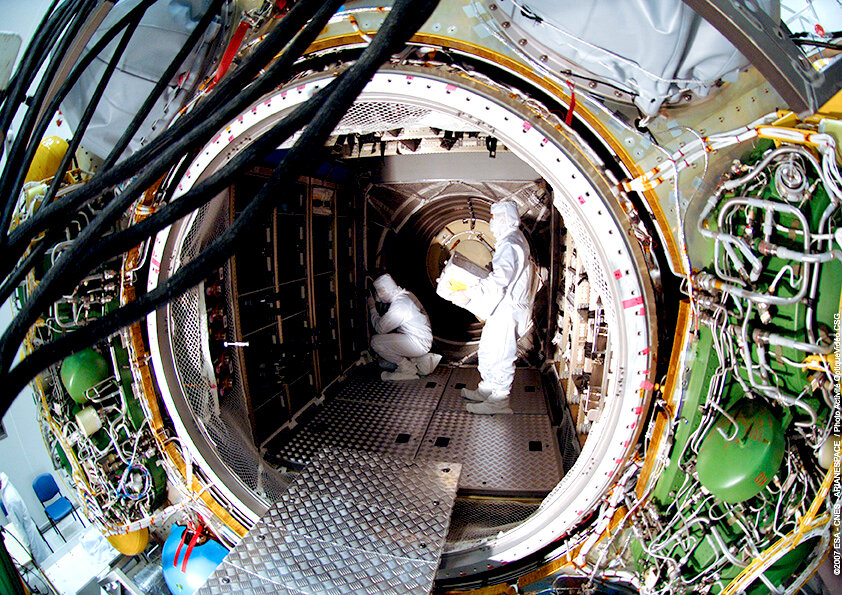
The Equipped External Bay of the Integrated Cargo Carrier held 22 spherical tanks of different sizes and colours. These tanks were used to resupply the Station with propellant for its propulsion system, water and gas (air or oxygen or nitrogen) for the crew. This cylindrical bay and its tanks were not visible from outside the ATV as they were hidden behind the interface linking the Cargo Carrier to the ATV Service Module.
Although ATVs were uncrewed, astronauts dressed in regular clothing could access the contents of the pressurised part of ATV during its attached phase with the International Space Station.
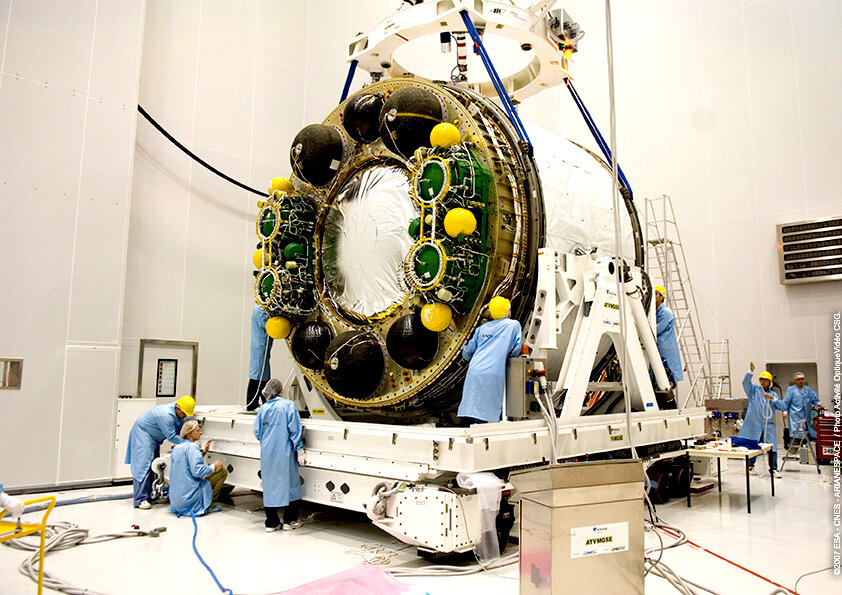
Up to two astronauts could work to unload supplies and conduct experiments, while the hatch remained constantly open. The pressurised module was designed to accommodate up to two crewmembers working for eight hours.
ATV's pressurised cargo section is based on the Italian-built Multi-Purpose Logistics Module (MPLM), which flew as a Shuttle-carried 'space barge', transporting equipment to and from the Station.
Air loaded in the ATV was released manually from the Cargo Carrier into the Station's atmosphere through the hatch.
External appearance
On the outside of the Cargo Carrier, ATV was covered with an eggshell-coloured insulating foil layer on top of meteorite protection panels.
The front cone contained the avionics and propulsion hardware:
- 2 telegoniometers, which continuously calculated distance and direction from ATV to the International Space Station
- 2 videometers, an image processing system able to compute distance and orientation of the Space Station
- 2 star trackers, which are able to recognise constellations in the sky
- 2 visual video targets are used by crew for visual monitoring of ATV's final approach
- 8 mini jets for attitude control
Russian docking system
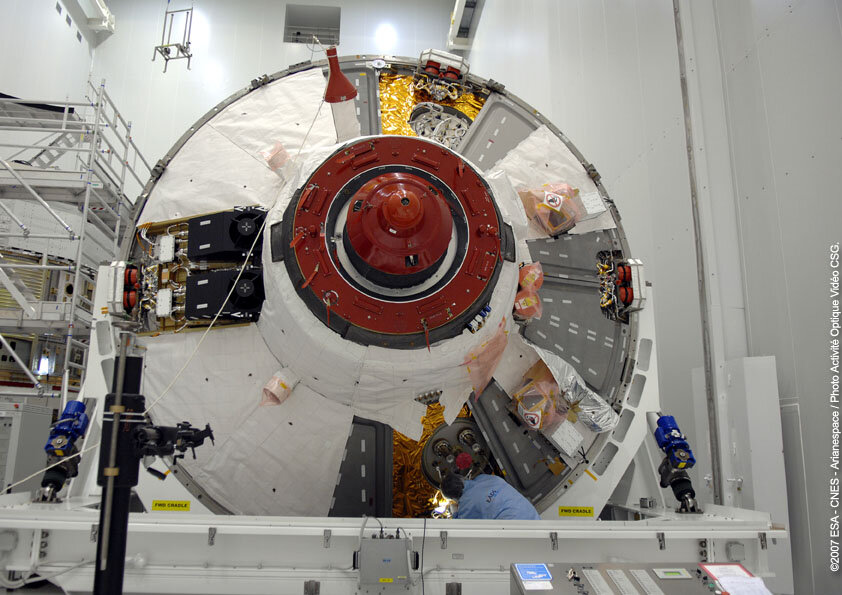
The nose of the Integrated Cargo Carrier contained Russian-made docking equipment and rendezvous sensors. The Russian docking system allowed for physical, electrical and propellant connections with the Station as well as providing access to the habitable module when docked.
With ATV securely docked, the Station's crew could enter the cargo section and remove payloads such as maintenance supplies, science hardware, and parcels of fresh food, mail and messages from family. Meanwhile, ATV's liquid tanks were connected to the Station's own plumbing to transfer their contents.
The front cone of the Integrated Cargo Carrier accommodated the 235 kg Russian docking system with its 80 cm-diameter hatch, its alignment mechanism and its one-metre-long extendible probe. During rendezvous the ATV was the active spacecraft and was equipped with an arrow-shaped probe mechanism. The Space Station has receiving-cone mechanisms at docking ports which are routinely used for Russian Soyuz and Progress space craft dockings.
The Russian docking system, which has been continuously refined since it was originally developed in the late 1960s for the Salyut space station programme, remains the worldwide state-of-the-art in docking mechanisms.