Ten ways 3D printing could change space
This close-up shows a titanium ball manufactured by 3D printing. ESA is investigating the potential of this promising new technology to transform the way space missions are put together.
1. Items impossible to make any other way
“This design is a perfect example of additive manufacturing (AM),” explains ESA materials engineer Benoit Bonvoisin. “These balls are hollow with a complex external geometry, making them incredibly light while remaining stiff. They simply could not have been manufactured in a single part, conventionally.”

With the idea that similar geometries could be used in future for ultralight satellite structures, the balls have been analysed in ESA’s Materials and Electrical Components Laboratory. Residue from the metallic beads used to clean the 3D-printed structure can be seen trapped within the ball lattice, showing the need for an improved cleaning process in future.
2. Computer designs translated to physical models
Instead of standard ‘subtractive manufacturing’ – where material is cut away from a single piece – AM involves building up a part from a series of layers, each one printed on top of the other. It is the difference from digging out a bunker to building a house.
The process starts with a computer-aided design (CAD) model, which is then sliced horizontally apart to plan its layer-based physical construction. Anything suitable for the printing process can be designed by computer then printed as an actual item, typically by melting powder or wire materials, in plastic or metal.

In February ESA hosted a ‘mapping meeting’ for the future development of AM for space at its ESTEC technical centre in Noordwijk, the Netherlands. Its 70 participants included representatives of 12 national delegations and the European Commission.
3. Novel design rules
“AM offers a totally different way of designing,” explains Laurent Pambaguian of ESA’s Materials Technology Section, coordinating the Agency’s AM research. “Traditional design rules are often linked to giving a cutting tool access to the bulk part – how do we remove the surplus material to produce the final item?
“AM, on the other hand, doesn’t mean we do away with all restrictions, but we are moving away for the traditional ‘design for manufacturing’ approach towards ‘design for need’.

“We also require fewer manufacturing steps, less material and energy – making it a greener process as well. The real challenge is to grasp the new AM design rules, and change our standard way of thinking accordingly, in order to maximise the benefits AM can bring us.”
4. Benefiting space, a low-volume industry
Laurent believes that AM, if applied well, can overcome many problems manufacturing for space has traditionally faced: “Space is a low-volume industrial sector, we need a relatively small amount of parts, but very well made. So, for instance, we might require only several kilos of a particular material, but then find it is only available to be purchased in 10-tonne bulks.

“Or there are certain processes that are effectively out of reach: take metallic injection moulding, which produces very good quality parts, but you might need to manufacture at least 100 000 to pay for the cost of the mould. So with AM we have the hope of replacing other technologies that are not affordable for us.”
5. Making models
Down on the ground, ESA engineers already make routine use of AM in various ways. Take the team at the Concurrent Design Facility, who use networked computer tools and multimedia tools for the rapid design of future space missions. They also have a plastic 3D printer at their disposal. As a virtual spacecraft takes shape on the screens before them, the team can also pass around a scale model of the same design, made out of the same plastic as Lego bricks.

And metallic 3D-printed parts commissioned from outside firms have also been used to refit or repair full-scale equipment in the ESTEC Test Centre, Europe’s leading collection of spaceflight simulation facilities under a single roof.
6. 3D-printed test items
But before AM parts can be employed on actual space missions, ESA’s materials engineers need to be confident that they can achieve the exacting quality levels needed. Back in 2009, when the Agency began this research, its starting point was to use AM to reproduce items that had actually flown in space.
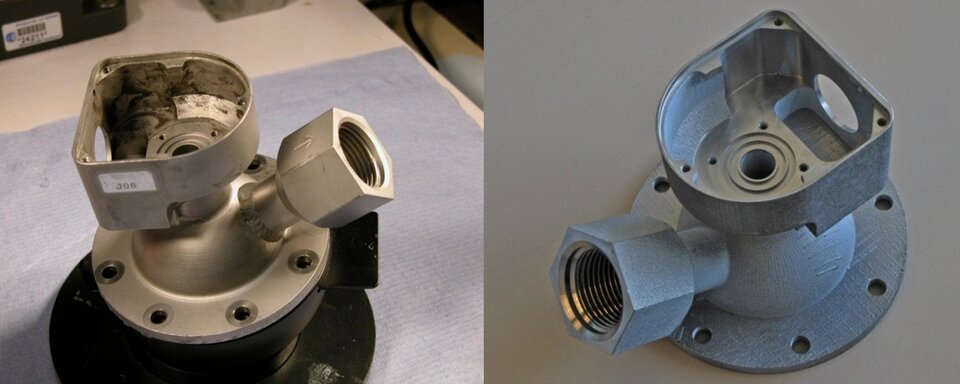
“The very first item we produced was a titanium copy of a stainless steel ‘woov’ (water on-off valve),” explains Laurent. “This has been flown on ESA’s Columbus Space Station module, as part of its plumbing.
“We choose the woov because it contains both thick and thin walls, as well as a weld. With our AM version we were able to remove the weld – an unwanted point of weakness – reproduce the part in titanium at an affordable cost and, through changing the material, reduce the item mass by 40%.”
7. RF filters and engine parts
Follow-up test items included an antenna support strut, where mass was reduced by 46% and a radio-frequency filter possessing an internal silver coating – normally produced by bolting halves together – had its mass reduced by 50% and its manufacturing time slashed by several weeks.
Its internal geometry was also made more wavy: the silver coating required to optimise its radio-frequency performance is far easier to apply than when dealing with sharp corners encountered in today’s state-of-the-art hardware. Such tailored design is another advantage of AM.

ESA’s Propulsion Engineering section also took an early interest in AM, as a way of building the extremely complex shapes required by rocket nozzles and combustion chambers. “We began by remaking a showerhead injector, with complex internal geometry and more than a hundred separate welds,” explains Matthew Smith.
“The biggest challenge for the selective laser melting metal AM technology we used was achieving the 150 micron-diameter holes studding the 25 mm-diameter showerhead, but we’re currently talking to suppliers that report capability to achieve this.”
8. Lightweight lattices
The same kind of honeycombed lattices demonstrated by the titanium balls offer a way of reducing the mass and cost of rocket chambers and nozzles. They can also improve their thermal resilience, considering engine temperatures can rise as high as 2500°C. Such lattices have a hugely increased surface area compared to standard solid items, enabling increased radiative cooling.

Similar AM-printed lattices are also being considered as more durable thruster catalyst beds, which will escape the typical degradation in performance of standard pellet-based catalysts over a propulsion system’s lifetime.
Or carefully-tailored AM lattices have been investigated for ‘propellant management devices’ – sponge-like elements inside a propulsion tank that help prevent bubbles and ensure steady thruster performance.
The broader potential of lattices to slash the mass of future satellite structure is also being considered.
9. Steps on the way to space
We’re still a long-way from the routine use of AM parts in space. Problems like material post-processing, surface coating and ensuring the necessary precision geometries still need to be solved. And new qualification standards have to be written – but progress is being made.
Occasional AM parts have already made it up to orbit: a 3D-printed plastic toolbox was flown up to Columbus last year.
NASA has announced plans to fly a plastic 3D-printing machine to the Station. Meanwhile, ESA and the European Commission have embarked on a project to perfect the printing of space-quality metal components. The AMAZE project – Additive Manufacturing Aiming Towards Zero Waste & Efficient Production of High-Tech Metal Products – involves 28 industrial partners across Europe.
10. Future potential
How might AM transform space missions in future? An ESA project to design a lunar base using 3D-printed local lunar rock demonstrates the broad span of its potential.

Manned missions could carry a 3D printer with them to ensure full self-reliance as they fly many months or years distant from Earth. Any broken item could be quickly and easily replaced. This approach has already been validated by ESA by manufacturing and functionally testing parts that have required fixing during past manned missions, including screws, clamps and even plastic gloves.
Or satellites in space could self-print new subsystems to provide new capabilities, in the same manner that today’s space probes are still having their software written on the way to their destination. Delicate parts could be manufactured on-orbit, avoiding the need to design around heavy launch loads.
Down on the ground, the possibilities are just as exciting: slashing the energy and mass needed for manufacturing could shrink the environmental footprint of the space industry hugely, the reason why AM is also of interest to ESA’s Clean Space initiative – tasked with reducing the space industry’s impacts on the environment.