Tapping into the design space of irregular geometry
Future space infrastructure – especially those built directly on other planetary bodies or in orbit – have to meet demanding conditions such as large temperature gradients and exposure to high-energy radiation. These constructions will require materials that are not only fairly easy to process and shape, but are also highly adapted to their environment. Materials that boast environment-specific physico-chemical properties, among others, tailorable mechanical properties like specific stiffness, Poisson’s ratio and damage tolerance1. However, being off-Earth severely limits the type of materials available for construction, which in turn constrains the realizable design space of future space infrastructure.
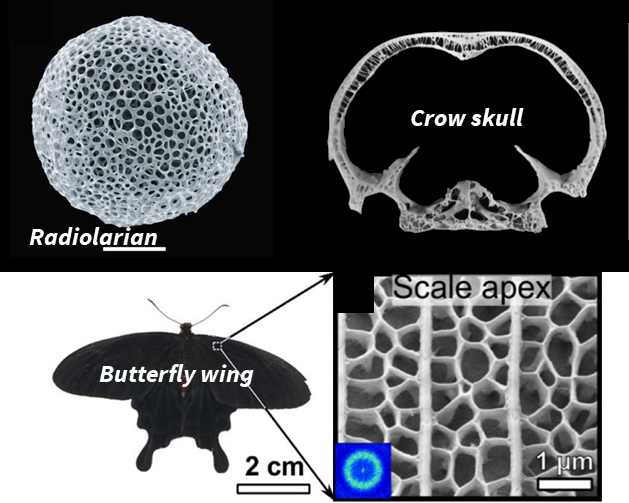
A promising solution for this dilemma can be found in additive manufacturing (3D printing) and architected metamaterials: 3D-printable materials comprising synthetic truss-based lattice structures, allowing changes to a 3D material’s properties by only adjusting the underlying lattice structure. In fact, over the last decade, the European Space Agency (ESA) has already been involved in pioneering the capabilities for 3D printing such lattice materials from a variety of space-relevant polymers, metals, and in situ planetary regoliths2,3. Looking into nature, such lattice materials can be found almost everywhere: bone, plant stems, dragonfly wings, coral, and radiolarians (Figure 1) are just some examples of natural lattice materials that showcase how intricate architecture is used to achieve extreme mechanical performance with a limited choice of constituents4. But different from human design – which is most often based on periodic patterns – nature employs lattices with a high degree of “controlled irregularity”. Despite their seemingly random appearance, natural lattices have been shown to possess surprising behaviours, e.g., high degrees of damage tolerance and defect engineering whilst being very light-weight5,6 – demonstrating that irregular designs are not just an “unwanted” side-effect of biological systems, but can actually unlock intriguing functional material properties. The freedom afforded by the geometry of 3D-printable irregular lattices has the potential to unlock a completely new design language for future space infrastructure. But there is a catch: this freedom comes with an overwhelmingly large design space – a space far too large to be navigated by human intuition alone.
In a recent project bringing together materials science and artificial intelligence researchers within ESA’s Advanced Concepts Team, a novel method was developed to help designers navigate through these treacherous waters. Combining ideas from artificial intelligence, computational neuroscience and materials science, we introduced a method for inversely designing irregular 3D lattices. This is to say, our method is able to find a unique structure with a desired set of mechanical properties completely autonomously. The method consists of two main components: a forward model that predicts material properties from the geometry of the lattice, and an inverse path, which adjusts local elements of the lattice using gradient-based optimization to achieve a new geometric design with desired material property. The proposed technique not only allows geometric changes by moving nodes or altering individual beam features (cross-sectional area, local composition, etc.), but it also enables adding or removing beams from the lattice altogether during the inverse design process.
In Figure 2, an example design is shown. Starting from the well-known hexagonal honeycomb (often seen in real engineering materials, Science Fiction movies and TV series alike), a vertical axial force is applied that predictably leads to transversal bulging as the material is compressed. We then set out to redesign this material with inverse design. Using our method, we are able to change the honeycomb’s lattice geometry until no outward bulging appears at all under the same load. After only 9 iterations with our method, an almost symmetric design is found that perfectly fulfils this criterion. To our surprise, the cell structure the algorithm found closely resembles a known tiling in materials science – the so-called re-entrant honeycombs – but tilted and shifted accordingly to obtain our prescribed material behaviour.
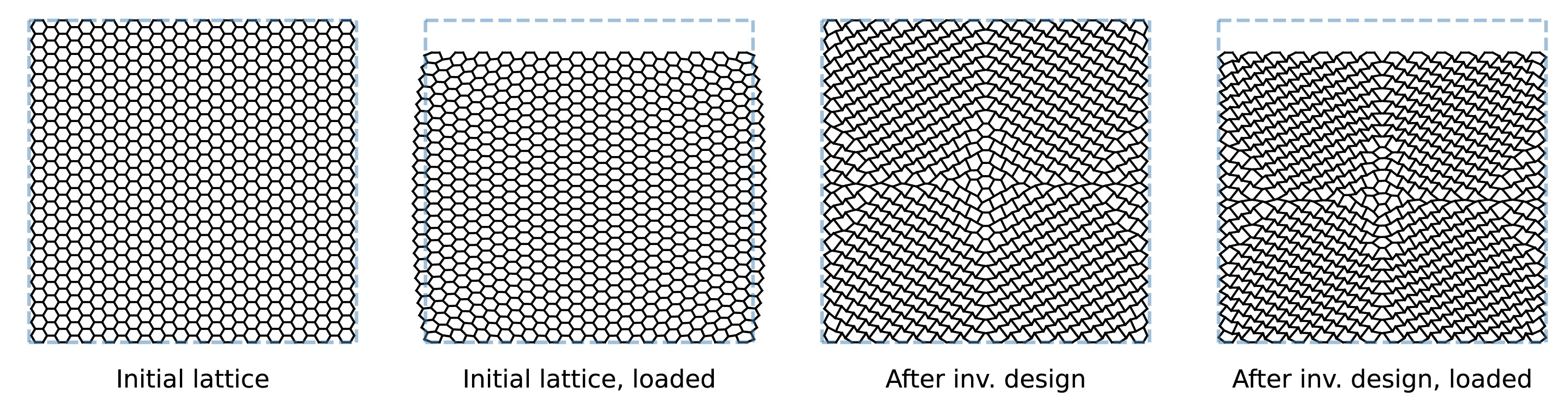
The results of the study have been published in the open access journal Cell Reports Physical Science (DOI: 10.1016/j.xcrp.2023.101586). The paper is also available on arXiv (DOI: 10.48550/arXiv.2304.05422). As a follow-up study, researchers in the ACT are currently looking into applying the method to so-called “Totimorphic lattices”7. These emerging class of lattices will be capable of re-organizing their topology on the fly, without the need for being 3D-printed anew.