100% bio-sourced thermoset composites tested for space
Combining high strength with low weight, corrosion-resistant and shapeable into almost any form, composite materials are a key ingredient of modern life: employed everywhere from aviation to civil engineering, sports equipment to dentistry – and also a vital element of space missions. But they have some less desirable aspects: made from petroleum products, they are non-renewable in nature and also non-recyclable. So ESA is working with Côte D’Azur University on a new breed of space-quality composites made from wholly sustainable sources.

As their name suggests, composites are made from two or more separate materials, combined together to obtain an optimal combination of physical characteristics. ‘Thermoset’ composites are among the most robust examples. They are made from resins which are blended with fibres or fillers for added strength – the same approach as adding steel piles concrete to make reinforced concrete – which are then ‘cured’ through heating, pressure or chemical reactions to solidify them.
Exploring alternatives
“The problem with the classical thermoset resins we use to make space-quality composites is that they are petroleum-based, so by definition they come from a non-renewable resource,” explains ESA materials engineer Ugo Lafont. “So we had the idea of exploring alternatives – could we use biomass as a new source of molecules for these resins, harnessing the same kind of chemical processes?

“And when we say biomass we don’t mean growing new crops especially for this purpose, but rather reusing existing bio-based material cheaply and efficiently – namely used vegetable oil, timber waste and oceanic algae.”
The idea came out of discussion with Professor Alice Mija of the Nice Institute of Chemistry (ICN) at Côte D’Azur University in France.
“It’s a very ambitious and challenging project – to produce 100% bio-based thermoset resins for space – which draws on a lot of different chemical, engineering and industrial expertises,” she comments.
“Obviously the desire for greater sustainability by avoiding the use of petroleum products is one important driver of this work. In addition one of the key chemicals used for thermoset production, bisphenol-A, is in the process of being restricted by the European Union’s Registration, Evaluation, Authorisation and Restriction of Chemicals, REACH, because of its hormone-altering and mutagenic properties. It has already been banned for food packaging products, and further restrictions will come in future.”

The cooperation takes the form of a part-sponsored PhD and now post-Doctorate research, supported through ESA’s Open Space Innovation Platform, sourcing promising new ideas for research from academia, industry and the general public.
Extreme challenges of space
Post-Doc researcher Roxana Dinu adds: “We’ve focused on space because if we can design materials to resist all the peculiar factors of the orbital environment – such as extremes of temperature and radiation as well as sustained hard vacuum encouraging unwanted ‘outgassing’ of fumes – then they should also be suitable for a very wide range of applications on Earth too, such as the aerospace, maritime and construction sectors.”
So far numerous 100% biobased monomers have been synthesized by Prof. Mija's group at laboratory scale, then their formulations into usable resins were studied and optimized. The space-qualification tests are currently ongoing by using project’s specialist facilities at ESA’s ESTEC technical Centre in the Netherlands as well as Thales Alenia Space in Cannes, a near neighbor of ICN- Côte D’Azur University.
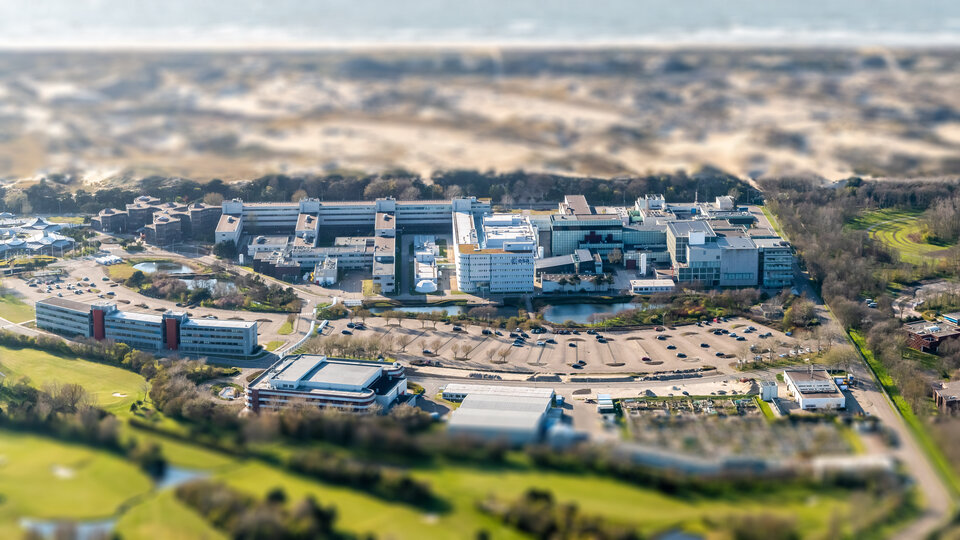
Scaling up – and going all natural
The next step in this three-year project will be to manufacture the composites at larger, demonstrator scale, then talk to companies about industrial production.
Ugo adds: “An important aspect of the project is that we want to adapt existing industrial processes for producing these new thermosets, we don’t want to have to reinvent the wheel.”
The project is also looking into the idea of harnessing natural materials for the other composite ingredients, resulting in 100% bio-based composites. “Conventional carbon fibres are not recyclable, so we are looking into the use of natural alternatives, such as plant fibres such as flax or hemp, for certain uses.”

The 3 Rs: reuse, recycle, repair
The great drawback of today’s thermoset composites is that they cannot be melted, reformed or dissolved, so are not recyclable. Disposing of them can prove challenging, potentially involving grinding them down to powder – while from 2025 the disposal of composite wind turbine blades in European landfills will be banned.
The project is looking into the potential of composites able to achieve the ‘3 Rs’ – reuse, recycle and repair.
Prof. Mija says: “100% bio-based composites are not inherently recyclable either – it comes down to the chemical formulation used to make them, but we are actively exploring reuse possibilities. We have used a nontoxic and easy to prepare solution, to recover vegetable fibres and recycle the 100% bio-based resin, which was then used for the production of a second generation of composites. The industry is eager for recycling solutions, so the potential here is enormous.”