Tailor-made composites for tougher space structures
An ESA-led project constructed a test cylinder using a novel method of laying down carbon fibre, then tested it to buckling point within a crushing machine that subjected it to the equivalent of 10 tons of force. The cylinder met its predicted specifications perfectly, outperforming a traditionally-made equivalent using the same constituent materials. The company involved, iCOMAT in the UK, has now been shortlisted for the 2022 JEC World Composites Innovation Award – recognised as one of the year’s global top three main innovations in the field of aerospace composites.

“I’m pleased for ICOMAT as our project partner, to receive this recognition from the organiser of the world’s top composites expo,” comments ESA materials and processes engineer Donato Girolamo. “I’m also happy that their work with ESA helped boost their profile, as a university spin-off competing with top composites companies possessing orders of magnitude higher R&D budgets, supplying leading aerospace names.”
Stronger than steel yet lighter than aluminium, carbon fibre reinforced polymer (CFRP) is used to manufacture everything from Formula 1 racing car bodies to wind turbine blades, high-end sports equipment to aircraft wings – and, increasingly, key elements of spacecraft and launchers. CFRP is typically made by casting epoxy resin with carbon fibres threaded through it for robustness, following a similar approach to steel-reinforced concrete.

“The key point about composite material is that it is not uniformly strong and stiff in all directions, but rather its strength and stiffness really depends on the direction its carbon fibres are laid down in,” explains ESA structures engineer Shumit Das, overseeing the project.
“Currently, a technique called ‘automated fibre placement’ exists that can lay down successive layers of fibres in complex geometries to increase stability and stiffness and delay buckling. The problem is that whilst this process is well established for laying carbon fibres in straight paths there is a lot of margin for error when trying to steer the fibres around curved paths or access holes designed into the part, which creates many small imperfections – such as gaps and overlaps. Potentially these can in turn weaken the entire design. The final buckling stability of the structure ends up very sensitive to the size and location of these small defects during manufacturing.”

As an alternative, ESA has been looking into the potential of ‘rapid tow shearing’, a technique that has been researched by the University of Bristol for more than a decade, but only marketed as an industrial solution by spin-off company iCOMAT, also based in Bristol, during the last three years.
“With standard composites the fibre plies are laid down in a single straight line,” explains Dominic Bloom, Business Development Manager of iCOMAT.
“What this means is you need multiple layers to address differing directions of strain along the underlying structure – so your first layer might be oriented at 0°, your second at 45°, your third at 90° and so on.
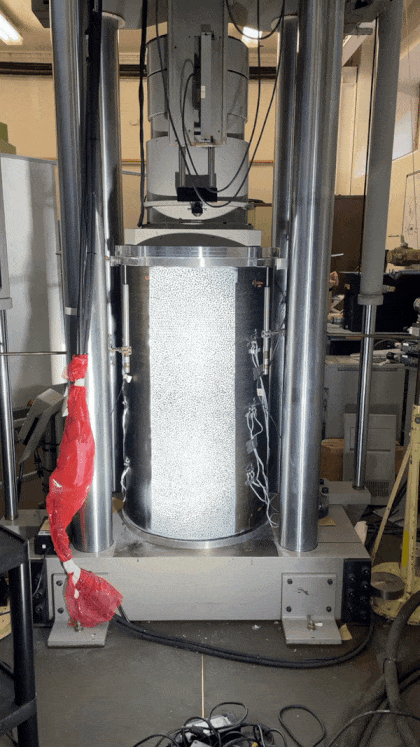
“With rapid tow shearing our tape-laying head can actually curve each ply in a continuous, carefully controlled way. This means we can continuously shear fibre tapes so that they can tessellate perfectly, with no gaps or overlaps.
“We also make use of wider and thicker tapes, putting down fewer layers to achieve an equivalent performance, or else achieve greater strength from the same amount of material.
“At the same time, our technology makes use of existing, well-understood, composite materials, rather than requiring anything new and can achieve very high deposition rates, boosting productivity.”
Donato adds: “This technique unlocks a whole new range of parameters in the design phase. By being able to curve our fibre lines along different directions across the same plane, we can really tailor our designs, ply by ply, to optimise the final structure’s buckling performance.”

To prove the potential of continuous rapid tow shearing, ESA worked with iCOMAT to produce two thin-walled cylinders 60 cm across and 110 cm tall, one using conventional automated fibre placement and the other using the novel technique. The University of Bristol contributed with ‘finite element analysis’ and structural optimisation of the new design, as well as designing and performing compression testing involving in excess of 100 kilo Newtons of force, equivalent to more than 10 tons of mass.
“We knew intellectually it was going to work, but we were still very nervous and excited to see what would happen,” adds Richard Hardy, Chief Operating Officer of iCOMAT.

“In the event, our tow-sheared cylinder demonstrated a 24% increase in the onset load needed to buckle it, an 8% increase in stiffness, and most of all a less than 5% difference in our software model in terms of its buckling load, mode shape and stiffness. This ability to match with the prediction is the most important part really, because by comparison the flaws introduced by automated fibre placement often means the physical design underperforms against its digital twin.
“The result is we need to use much less fibre – and by extension less CO2 – to achieve equivalent performance, making existing carbon fibre structures lighter and more cost effective, offering lots of potential for space as well as terrestrial sectors.”

De-risking technology for space
This ‘Fibre Steering for Lightweight and Cost Efficient Space Structures’ project was supported through ESA’s General Support Technology Programme, GSTP, converting promising engineering concepts into a wide variety of usable products.
Shumit adds: “This project came through our De-Risk element of GSTP, offering an early opportunity to demonstrate the most important aspects of new leading, edge concepts with relatively low maturity and carrying higher risk, in preparation for a full GSTP project. What we have done, based on ESA’s Technology Readiness Level yardstick, is prove the technology to laboratory scale. In our planned follow-on project with iCOMAT we would like to go further with larger-scale test parts, to get closer to flight readiness.”
Evangelos Zympeloudis, CEO of iCOMAT comments: “It was the UK delegates to ESA who helped make this project possible, as well as the UK Space Agency, by showing early belief in the technology and then making the initial contacts with ESA. We’re looking forward to collaborating further with ESA on the next steps.”