Precision deployer to put Hera’s CubeSats into asteroid orbit
Dutch firm ISISPACE has manufactured more than 600 cereal-box sized ‘CubeSat’ satellites, plus nearly 200 deployment systems used to release them into orbit. Of all of these, the pair of Deep Space Deployers it has overseen for ESA’s Hera asteroid mission for planetary defence have been by far the most challenging. The two systems need to keep their nanosatellite cargo alive and healthy, before releasing them on a precisely staged basis – at a velocity of just a few centimetres per second. Any faster and Hera’s CubeSats would risk getting lost in space.

Once Hera travels to the Dimorphos asteroid it will not go there alone. It will carry with it two CubeSats to gather additional data on its target: the Italian-led Milani CubeSat is equipped with a hyperspectral imager to perform mineral prospecting of the body’s surface while the Luxembourg-led Juventas CubeSat will perform the first subsurface radar probe of an asteroid, going on to touch down and measure surface gravity levels.
To keep these nanosatellites in good health through Hera’s two-year cruise phase through deep space and then to check out their independent functioning before releasing precisely as required within the asteroid’s ultra-low gravitational field, the mother spacecraft is equipped with a pair of Deep Space Deployers, built into opposing ends of Hera’s topside.

Slow release in asteroid orbit
Standard deployers employed for CubeSat missions to low-Earth orbit serve as a kind of supportive exoskeleton for these tiny items during their turbulent ride to space, then inject them into orbit. Hera’s Deep Space Deployers must operate for much longer. They then have to release their cargo in a gradual and carefully engineered manner.
“In complexity terms, our Deep Space Deployer design is equivalent to another onboard instrument,” explains Hera’s ESA system engineer Franco Perez Lissi. “Instead of releasing its CubeSat with a big spring like a standard deployer, pushing away from the parent at around two metres per second, we need to release two orders of magnitude more slowly, because the asteroid gravity is less than a millionth of Earth’s. If we release any quicker then the CubeSat could well miss the asteroid altogether.

“In addition, the two DSD will be used to communicate with their CubeSats, throughout Hera’s approximately two-year voyage to Dimorphos, exchange telemetry and telecommands, update software, charge batteries, test reaction wheels and perform final health checks.”
Ralph Slootweg, lead mechanical design engineer at ISISPACE adds: “Then, when we get ready to deploy each CubeSat, this does not happen all at once. We begin with springs that push the CubeSat up to the top of the DSD, but it will remain linked to Hera through an umbilical for power and communications. Over an approximately 24-hour period each CubeSat will have its systems activated and checked out while exposed to space – including the inter-satellite links that will be used to communicate back with Hera – before undergoing their final release, intended to occur not only slowly but also precisely, minimising any imparted rotation which would need precious onboard cold-gas propellant to correct.”
Check-out before deployment

Ralph notes that this is very much a change from the standard quick-release approach : “The reason for deploying this way is that in Earth orbit there are ground stations available to communicate immediately with newly-deployed CubeSats. Out at Dimorphos there will only be Hera.”
The DSD’s CubeSat Release System that will give each CubeSat their final push away had to tested in terrestrial gravity, which meant employing a pendulum-based rig plus high-speed cameras to validate that the desired velocity would be reached at Dimorphos.
The overall DSD design also had to be subjected to a full qualification campaign, including environmental testing to check if it can survive the launch and cruise phases.

ESA Mechanisms engineer Ewelina Ryszawa comments: “This was certainly a challenge – we experienced a failure during the vibration test, so we had to redesign some subsystems: add in extra margin, with a stronger actuation spring and reducing friction elsewhere. It ended up a good problem-solving exercise.”
Interface with Hera
The DSD also serves as the de-facto interface between Hera and its CubeSats – a crucial role because these two types of spacecraft have been built to very different standards.
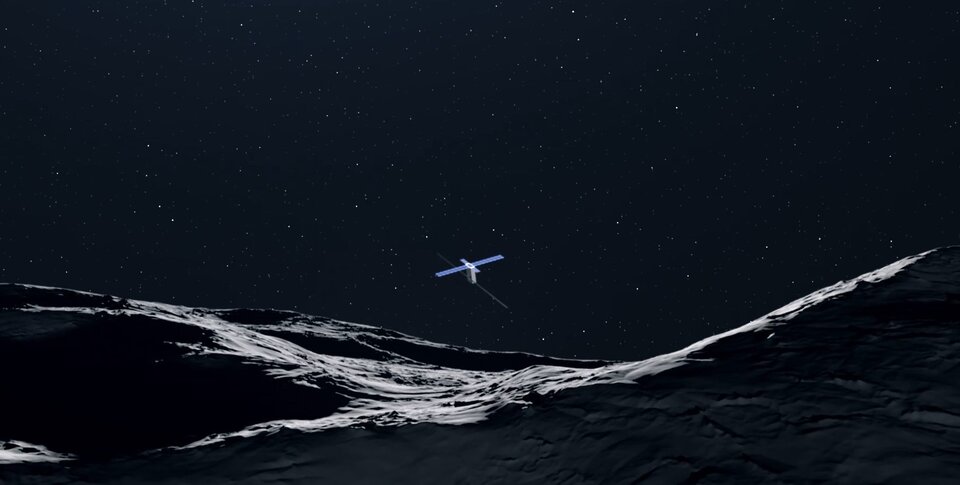
“At the base of each DSD is its Life Support Interface Board, LSIB, which is the connection between Hera and each of the two CubeSats,” explains Tatsuo Shimizu, LSIB project manager and designer at Finland’s Kuva Space. “The LSIB converts signals and power voltage between the two sides, and also performs isolation in the event of any CubeSat failure. Essentially, all of Hera’s interaction with the CubeSats in their DSDs takes place via the LSIBs.”
Tatsuo worked hard through the COVID-19 pandemic to meet the LSIB’s strict deadline, having to spend thousands of euros to phone around component suppliers in response to supply chain disruptions, adapting the LSIB design accordingly.
Maria Hieta, overseeing product assurance for the LSIB at the Finnish Meteorological Institute, FMI, adds: “While Hera is built using traditional space-grade components, following all applicable European Cooperation on Space Standardization, ECSS, standards, miniaturised CubeSats can use lower grade parts and take more risks in the design.

Access the video
“Overall this is a strength, but the Hera team needs to be sure that any CubeSat problem would not spread to the main spacecraft as well, such as an overvoltage. For this reason, the LSIB is built with space qualified parts following the same standards as Hera. Our institute has plenty of experience in developing hardware to ECSS standards, so we undertook the product assurance for the LSIB, while Beyond Gravity in Finland performed the soldering.”
The DSDs have now been accepted, delivered and integrated aboard Hera. Once the CubeSats complete their testing, they will be installed aboard the DSDs for integrated testing.
Find out more about the fascinating asteroids populating our Solar System, the space missions seeking to explore them and the ways Earth is being safeguarded from impact threats in the webcast for the UN-sanctioned Asteroid Day this Friday, 30 June.