Readying ESA's 'garbage truck': Robin Biesbroek interview
Robin Biesbroek runs system-level activities for Clean Space, meaning that he takes care of studies focused on the design of a mission for space remediation – part of Clean Space Branch 4: Technologies for Space Debris Remediation.
You are in charge of the e.Deorbit study. Can you explain us what it is about?
e.Deorbit is a mission with the objective to capture a large item of space debris and remove it out of the LEO protected zone. With large space debris we mean an object of at least 4000 kg. Several independent studies have indicated that the most effective solution to stabilise the growth of space debris is to remove large objects from crowded orbits, such as polar or near polar orbits within the 600 km to 800 km altitude range, and e.Deorbit is doing exactly that.
The e.Deorbit satellite has to acquire a similar orbit to the space debris first, using absolute navigation. Then it needs to rendezvous with the debris, using relative navigation. Keep in mind that the space debris was never designed to be ‘tracked’ or captured by another satellite, so we call this an ‘uncooperative target’.
Then the e.Deorbit satellite needs to capture the debris, and after having achieved a firm connection, remove it from orbit. This can be done by de-orbiting it into the atmosphere, or by re-orbiting it above the LEO protected zone, which is a zone around the Earth spanning to an altitude of 2000 km.
Within the e.Deorbit study we try to find one rigid capture solution and one flexible capture solution to de-orbit the space debris. A third mission option is to re-orbit the debris in a less trafficked orbit. We have three contracts with industry to design the capture method and the spacecraft platform, for all three mission options.
Can you explain the key challenges involved in this work?

A major challenge is the design of a satellite-based capture system, in order to catch space debris. Many options exist and all have their advantages and disadvantages, as well as their impact on the entire satellite system.
Examples one can think of are a robotic arm to catch the debris, or another form of clamping mechanism to grab on to it, or catching the debris using a net similar to what fishermen use, or by shooting a harpoon into the debris.
We have to take many things into account when doing a trade-off, such as how costly it will be to develop, how robust it will be to changing circumstances, how heavy it is, how strongly it can hold the debris, how easy it is to perform a second try if the first try fails, and how much it fulfils the requirement to not create any extra debris.
So as you can see, many aspects influence the choice. Many technologies of this mission are new, as nobody has ever removed debris from orbit, so another challenge is to keep the cost down. We have done a lot of studies on capture techniques within ESA’s Concurrent Design Facility (CDF), and it is important that we transfer our knowledge to industry.
Currently we are working with industry to downscale the number of options to two or three, and by the end of the summer I hope to have one preferred solution.
How did you first get involved in Clean Space?

I have been involved since the beginning. Before Clean Space started, I was asked to be the team leader for a study called ‘Ecosat’ in the CDF. In this study we looked at ideas and methods to reduce the environmental footprint of space missions. It was one of the forerunners of the Clean Space initiative. I liked it as it was very different to any other CDF study we had done. Clean Space started as a combined effort of several people, most of them people who also participated to Ecosat, and I decided to stay involved.
In the meantime I was leading studies on Active Debris Removal in the CDF so it was natural to lead the e.Deorbit CDF study in 2012. After the CDF study had completed, I became study manager for the Active Debris Removal studies. We did several assessment studies with industry in 2013, along with business plans for future debris removal. Now in 2014 we are running the phase A design, and we aim to start the B1 phase as well.
What is your opinion of the overall Clean Space initiative?

Clean Space fits within the current global trends towards a more sustainable environment, I think. The entire world is focussing more and more on a greener environment, cleaner forms of transportation, and better waste processing (or even removal of waste!), and it’s time to start considering space as our environment.
I have to admit that Clean Space evolved quicker than expected, and I’m sure that the motivation of the people involved helped here. In my opinion, we have a great time behind Clean Space, so it’s motivating and even fun for everybody to work for Clean Space.
How do you summarise Clean Space for your non-technical friends and family?
I explain how we are improving the environment on Earth, giving examples like greener rockets and cleaner materials for satellites. When I speak about e.Deorbit, I often explain it as a large ‘garbage collection truck’ in space.
How did you get your start in the space business?
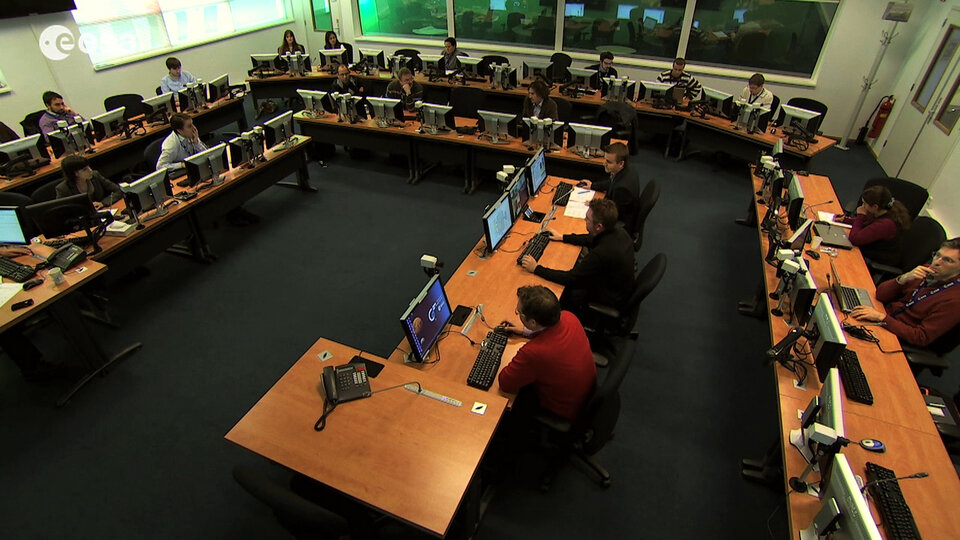
After seeing the 1980s movie ‘Into the Night’ I realised that there is actually a job title of aerospace engineer! So I started studying aerospace engineering at Delft University of Technology.
There, I met ESA astronaut and professor Wubbo Ockels, and he accepted to become the graduate professor for my Master of Science thesis assignment. The subject was to investigate the use of genetic algorithms for space applications, in particular for orbit dynamics of tethered systems.
Back in 1995 this was a new form of optimisation. I was able to study this thesis on-site at ESTEC, through which I met many colleagues who became interested in the topic.
After graduation and an external traineeship in French Guiana, I was offered a position as a Young Graduate Trainee (YGT), where I would not only pursue my research in genetic algorithms for space applications, but even work on a real mission called TEAMSAT, which was both developed and launched within my year as a YGT. Following that year I formed my own company and started developing trajectory optimisation software, which I would sell commercially to many space companies all over the world, and even to several sites at NASA. But I also kept supporting ESA, in particular the new CDF in the fields of system engineering and as team leader. Since 2010, I have been an ESA staff member at the CDF.
What has been your biggest surprise about working in the space business?

Two things. First of all the people. From the moment I arrived as a student people have been very kind and supportive, always taking me seriously. Even later as a company I noticed this. I could sit together with my customers at NASA or European primes and try to help them solving complex trajectories with my tools, and they were keen on taking my advice into account.
I even made many friends in this space community, and also in particular in the Clean Space team. This was a very pleasant surprise.
The second surprise is how advanced we, in the space business, still are with respect to other industries. I am a big fan of sports cars and see the developments there which are sometimes based on space applications that are already used in the space business for many years. Or look at the billion pixel camera aboard Gaia, which is another amazing advance in technology. It will take a long time before we get one billion pixels in our phone cameras!
How do you see Clean Space evolving in future?
I stopped predicting the future because I’m never right about it, but I would like to see Clean Space fully integrated into spacecraft or rocket design. For example, where trade-offs of materials take into account the environmental aspect. Or a spacecraft and launcher design that minimises waste, or even gets rid entirely of waste. Of course I would like to see ESA performing the first Active Debris Removal. This certainly would put European space industry into a leading role when it comes to cleaning up our environment, both on Earth and in space.